70%的产品成本在图纸阶段就被锁定。DFMA教你“边画图边算成本”,让好做、好装、低成本从第一笔线条开始;再叠一层DFEMA防错保险,设计与风控一次到位。
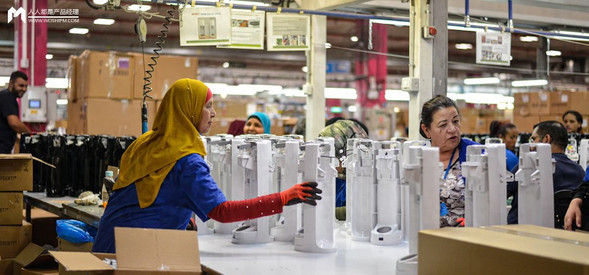
DFMA(Design for Manufacturing and Assembly)是一个强大的集成化工程方法论,其核心目标是在产品设计的最早期阶段就充分考虑制造和装配的约束、成本和效率,从而优化整个产品开发过程,实现高质量、低成本、易于制造和装配的生产制造产品。
DFMA 让设计师在画图纸的时候,就时刻想着“这东西好不好做?好不好装?成本高不高?”,而不是等到设计定型了才交给制造部门去头疼。
01 DFMA的组成
DFMA由可制造性设计(DFM)和可装配性设计(DFA)两部分组成。
DFM (Design for Manufacturing – 面向制造的设计):优化零件加工工艺、材料选择及结构设计,降低制造复杂度(如减少加工步骤、简化公差要求)。
关键焦点在于优化单个零部件的设计,使其能够以最低的成本、最高的质量和可靠性,使用选定的制造工艺(如注塑、冲压、铸造、机加工、3D打印等)高效地生产出来。
具体实现方案包含:简化零件几何形状、选择合适的材料和工艺、减少材料浪费、标准化、减少二次操作。
- 简化零件几何形状:避免不必要的复杂特征、深孔、尖角、薄壁等。
- 选择合适的材料和工艺:材料特性(强度、刚度、耐热、耐腐蚀等)必须满足功能要求,且与选定的制造工艺兼容(如塑料的流动性和收缩率)。同时考虑工艺能力,设计特征(如公差、表面粗糙度)必须在选定工艺的实际能力范围内,过严的公差会显著增加制造成本。
- 减少材料浪费:优化排样(冲压、激光切割)、减少机加工余量、考虑材料利用率。
- 标准化:使用标准件(螺栓、螺母、轴承)和标准原材料尺寸。
- 减少二次操作:设计应尽量减少或消除后处理步骤,如去毛刺、额外的热处理或表面处理。
DFA (Design for Assembly – 面向装配的设计):简化装配流程,减少零件数量(如通过卡扣替代螺丝),优化装配顺序和人机工程。
关键焦点在于优化产品的设计,使得所有零部件能够以最低的成本、最短的时间、最高的可靠性、最少的错误组装成一个完整的产品。
具体实现方案包含:最小化零件数量、确保装配的简易性、设计防错、简化紧固、提供无障碍的装配路径、模块化设计、标准化装配方向、自上而下的装配。
- 最小化零件数量:这是DFA最核心、最有效的原则。通过功能分析,质疑每个零件存在的必要性,考虑合并零件或设计多功能零件。零件越少,装配成本越低,潜在故障点越少。
- 确保装配的简易性:设计应易于抓取、移动、定位、插入和紧固零件。避免需要特殊工具或复杂操作的装配步骤。
- 设计防错:零件只能以一种正确的方式安装(Poka-Yoke)。使用不对称设计、定位销、键槽等防止错误装配。
- 简化紧固:减少紧固件数量和类型(标准化),优先选择卡扣、压配、焊接、粘接等更快的连接方式替代螺丝。
- 提供无障碍的装配路径:确保装配工具有足够的操作空间,零件可以顺畅地按顺序装配,避免视线阻挡或需要翻转产品。
- 模块化设计:将产品分解为独立的功能模块,便于并行制造、测试、维修和升级。
- 标准化装配方向:尽量使所有装配操作都在同一方向(如从上向下)进行。
- 自上而下的装配:理想装配顺序是从基础件开始,逐步向上和向外添加零件,避免在装配过程中需要反复翻转产品。
DFX是Design for X(面向产品生命周期各/某环节的设计)的缩写。其中,X可以代表产品生命周期或其中某一环节,如装配(M-制造,T-测试)、加工、使用、维修、回收、报废等,也可以代表产品竞争力或决定产品竞争力的因素,如质量、成本(C)、时间等等。
DFX要求在产品开发过程中和进行系统设计时不但要考虑产品的功能和性能要求,而且要考虑与产品整个生命周期相关的工程因素,只有具备良好的工程特性的产品才是既满足客户需求,又具备良好的质量、可靠性与性价比的产品,这样的产品才能在市场得到认可。
02 DFMA重要作用
DFMA具有显著降低成本、缩短上市周期、提高产品质量和可靠性、提升制造效率和灵活性、简化供应链管理、促进并行工程的重要作用。
- 显著降低成本:降低零件成本、装配成本、模具/工装成本、整体产品成本。
- 零件成本:减少零件数量直接降低原材料、采购、库存管理成本。优化设计降低单个零件的制造成本。
- 装配成本:简化装配步骤、减少紧固件、缩短装配时间直接降低人工成本。减少装配错误也降低了返工和报废成本。
- 模具/工装成本:简化的零件设计通常意味着更简单、更便宜的模具。
- 整体产品成本:据统计,产品约70%的成本在设计阶段就被锁定。DFMA在源头控制成本,效果最显著。
- 缩短产品上市时间:早期发现并解决制造和装配问题,避免后期昂贵的工程变更;简化的设计和装配流程加速了生产准备和爬坡阶段;减少设计迭代次数。
- 提高产品质量和可靠性:减少零件数量和装配步骤意味着更少的潜在故障点;防错设计减少了装配错误;更稳健的设计(考虑工艺能力和公差)提高了产品的一致性和耐久性。
- 提升制造效率和灵活性:简化的零件更易于自动化生产和装配;更少的零件和更简单的装配线降低了生产复杂性;模块化设计方便了生产线的配置和产品的变型。
- 简化供应链管理:减少零件数量和种类简化了采购、仓储和物流;标准化零件提高了采购议价能力和库存通用性。
- 促进并行工程:DFMA要求设计、制造、工艺、采购等团队早期紧密协作,打破部门壁垒,实现信息共享和共同决策。
03 DFMA实施流程
DFMA实施流程主要包含:组件跨职能团队、明确产品功能和要求、初始设计概念、应用DFMA分析、优化再设计、迭代、成本估算与验证、定案与输出。
组建跨职能团队:包括设计工程师、制造工程师、工艺工程师、装配工程师、采购、质量工程师等。
明确产品功能和要求:清晰定义产品必须实现的核心功能和性能指标。
初始设计概念: 设计师提出初步想法。
应用DFMA分析:
- DFA分析:对初始设计进行功能分析,识别冗余零件,计算理论最小零件数,评估装配效率(装配时间/理论最小装配时间),识别装配难点和风险点(如难抓取、难定位、需要工具、视线受阻等)。
- DFM分析:评估每个零件的可制造性。选择的制造工艺是否合适?特征是否容易加工?公差是否合理?材料是否最优?是否可以利用标准件?是否存在不必要的加工步骤?
优化再设计: 基于分析结果,团队共同讨论并制定优化方案:合并或消除零件、简化零件几何形状、改变材料或制造工艺、改进连接方式(减少或简化紧固件)、设计防错特征、优化装配顺序和路径。
迭代: 对优化后的设计再次进行DFMA分析,可能需要多次迭代以达到最佳效果。
成本估算与验证: 对优化后的设计进行详细的成本估算,并与原方案对比。制作原型进行制造和装配验证。
定案与输出: 确定最终设计方案,输出完整的设计文档(图纸、BOM、工艺文件等)。
04 DFMA和DFEMA的区别
DFMA(面向制造与装配的设计)与DFEMA(设计失效模式及后果分析)是产品开发中的两大核心方法论,二者既有显著区别,又存在紧密联系。
DFMA,主要是在设计定型前,聚焦制造与装配可行性,应用设计准则(如零件简化、防错设计、公差分析),通过优化设计以提升可制造性(DFM)和可装配性(DFA),输出零件数量优化方案、装配工序简化报告,实现降本增效(减少零件、简化工艺、缩短装配时间)的目标。
DFEMA,主要是在设计概念启动阶段,通过风险量化(严重度S×频度O×探测度D=RPN值)的方法,识别设计阶段的潜在失效模式,输出失效模式清单、预防措施、检测控制计划,分析其后果与风险,达到预防风险(确保可靠性、安全性)的目标。
首先,二者均强调在设计初期介入,避免后期修改的高成本,DFMA通过简化设计减少制造复杂度,间接降低失效风险;DFEMA则直接锁定设计缺陷;其次,在汽车行业APQP(产品质量先期策划)中,二者流程协同,DFEMA先行分析可靠性风险,DFMA紧随其后优化制造与装配;然后,二者工具互补,DFMA的防错设计(如防呆结构)直接降低DFEMA中的失效频度(O值),DFMEA输出的高风险项(如RPN>100)可指导DFMA优先优化相关部件。
DFMA 不仅仅是一套工具或方法,更是一种设计哲学和系统性的产品开发策略。通过在产品设计的最源头(概念和详细设计阶段)就深度整合制造和装配的考量,驱动设计的简化(零件数量最少化)和优化(零件易制、产品易装),从而带来巨大的商业效益:降低成本、缩短周期、提升质量、增强竞争力。
本文由人人都是产品经理作者【壹叁零壹】,微信公众号:【壹叁零壹】,原创/授权 发布于人人都是产品经理,未经许可,禁止转载。
题图来自Unsplash,基于 CC0 协议。