在现代企业运营中,库存就像一面镜子,既映照出供应链的健康度,也折射出资金的使用效率。据统计,制造企业的库存成本通常占总资产的 20%-30%,零售企业更是高达 40% 以上。然而,传统库存管理中 “账实不符”“呆滞料堆积”“紧急缺料” 等问题频发,根源在于缺乏系统化的分析框架和数字化工具。ERP(企业资源计划)系统作为企业数字化的核心载体,其库存管理模块的设计逻辑,正是为了破解这些难题 —— 通过多维度数字化建模、智能化分析和跨模块协同,将库存管理从 “经验主义” 推向 “数据驱动”。
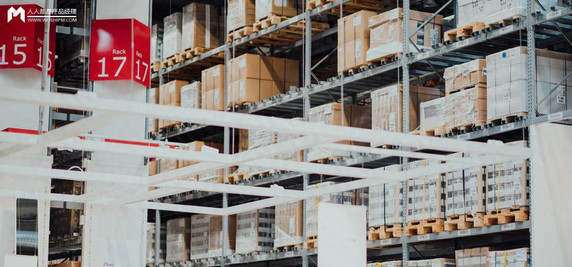
库存管理的第一步是 “看清库存”,而清晰的分类是基础。ERP 系统对库存的数字化建模,正是围绕货品类别、存货地点、账务状态、采购来源这四个核心维度展开,构建起立体的数据网络。
货品类别维度的设计需兼顾行业特性与管理颗粒度。在 ERP 系统中,这通常体现为 “多级分类编码体系”:比如电子制造企业可按 “元器件 – 组件 – 成品” 三级分类,每个层级关联特定属性(如元器件的规格、耐受温度)。这种结构化设计既满足了财务核算的汇总需求,又支持仓储拣货的精细化查询。
存货地点的数字化则突破了物理空间的限制。ERP 系统会将仓库、货位、区域等空间信息转化为编码,与货品信息绑定。例如,一个汽车零部件企业的 ERP 系统中,同一种火花塞可能同时存在于 “上海总仓 A 区货架 3”“武汉分仓临时周转区”“在途运输 B 批次” 三个地点维度,系统通过实时更新地点状态,避免了传统纸质记录中 “货在哪” 的模糊性。
账务状态的设计是 ERP 系统连接财务与业务的关键。系统会实时同步 “可用库存”“已分配库存”“待验库存” 等状态:当销售订单生成时,系统自动将对应数量从 “可用库存” 转为 “已分配库存”;当采购货品入库质检时,先进入 “待验库存”,合格后才转为 “可用库存”。这种实时联动确保了账实一致,避免了 “超卖” 或 “重复入库”。
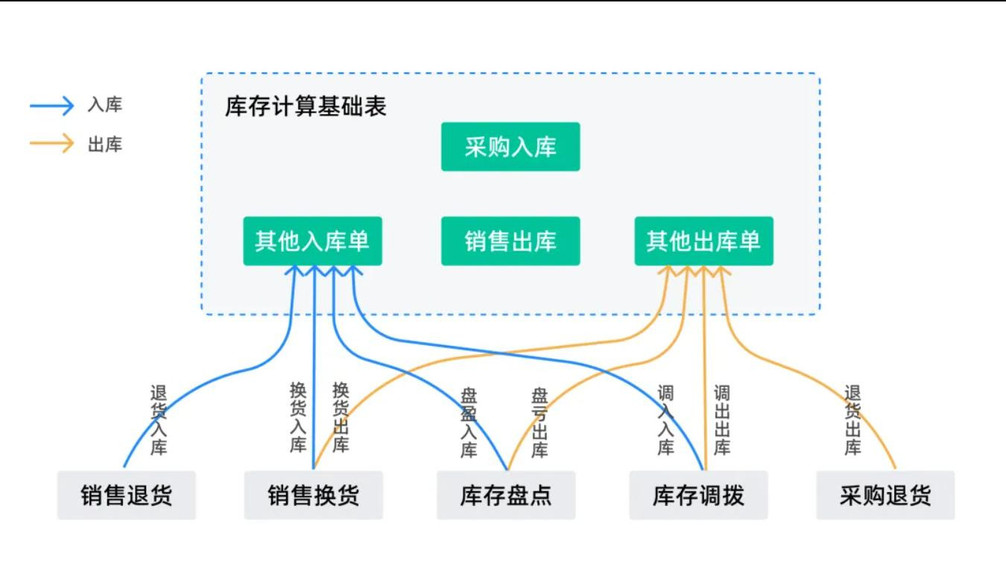
采购来源维度则实现了供应链的追溯性。ERP 系统会记录货品的供应商、生产批次、采购订单号等信息,形成 “从供应商到仓库” 的全链路数据。当出现质量问题时,系统可通过采购来源快速定位问题批次,甚至反向追溯至供应商的生产环节,这在食品、医药等强监管行业尤为重要。
这四个维度并非孤立存在,ERP 系统的核心价值在于支持 “多维度交叉分析”。例如,企业可查询 “来自甲供应商的 A 类电子元件在上海仓的待验库存数量”,这种精准查询能力为后续分析奠定了数据基础。
三大核心分析方法的系统实现逻辑
清晰的分类只是起点,ERP 系统的真正威力在于通过内置的分析模型,将原始数据转化为管理决策依据。库存风险系数、ABC 分类法、库存周转率这三种核心方法,在 ERP 系统中有着明确的设计逻辑。
库存风险系数的计算是识别呆滞库存的关键。ERP 系统会自动整合货品的库龄、历史销售频次、保质期(如适用)、市场需求变化等数据,按预设算法生成风险系数。例如,某快消品企业的系统中,“库龄超过 90 天且近 3 个月无销售” 的货品会被标记为高风险,系数大于 0.8 时触发预警。系统还会区分 “绝对呆滞”(如过时的电子配件)和 “相对呆滞”(如季节性商品),为处理策略提供依据 —— 前者可能触发折价清仓流程,后者则提示调整仓储位置以减少动线成本。
ABC 分类法的数字化实现让管理优先级一目了然。传统人工分类不仅耗时,还易受主观因素影响,而 ERP 系统会基于 “销售额占比”“利润贡献” 等量化指标自动划分:A 类货品(通常占数量的 10%,贡献 70% 销售额)会被标记为 “重点保障”,联动采购模块设置更高的安全库存;C 类货品(占数量的 50%,贡献 5% 销售额)则触发 “按需采购” 策略,甚至自动提示与供应商协商 JIT(准时制)供货。某机械制造企业通过 ERP 的 ABC 分类功能,将轴承等 A 类零件的库存周转天数从 45 天压缩至 28 天,同时将低值易耗品的资金占用降低了 30%。
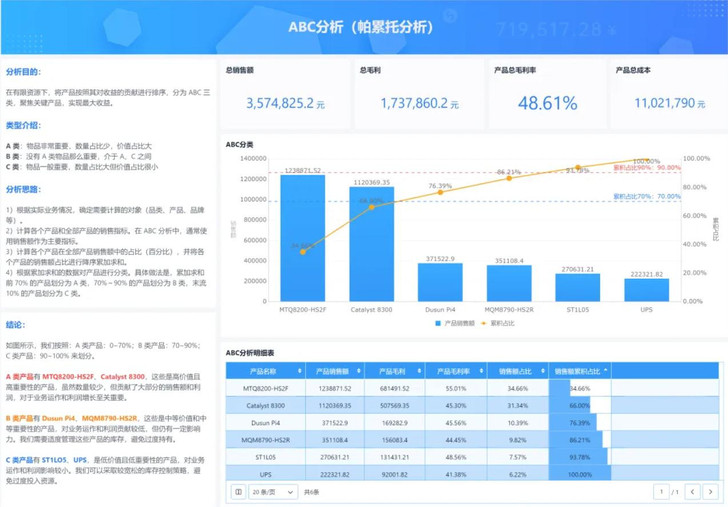
库存周转率的实时计算则直观反映了库存流动性。ERP 系统会动态抓取 “当期出库总成本” 和 “平均库存金额”,自动计算周转率并生成趋势曲线。与手工计算不同,系统能实现 “多维度周转率分析”:既可以看全品类的整体周转率,也能按部门、区域、产品线拆分,甚至对比不同供应商货品的周转效率。例如,当发现某区域的家电产品周转率连续下滑时,系统会自动关联该区域的销售数据,排查是促销不足还是库存结构与当地需求不匹配。
从问题溯源到系统解决:ERP 的协同设计思维
库存问题从来不是孤立的,采购预测失误、生产计划不稳、销售判断偏差等业务环节的漏洞,最终都会在库存数据上显现。ERP 系统的设计精髓,在于通过模块协同将这些问题扼杀在源头。
针对采购预测失误,ERP 系统会构建 “销售 – 预测 – 采购” 的联动模型。销售模块的历史数据和市场趋势分析会自动导入预测模型,生成初步采购需求;生产模块的 BOM(物料清单)会拆解原材料需求,与现有库存比对后生成净采购量;采购模块则根据供应商的交货周期和最小订单量,优化采购批次。某服装企业通过这种联动,将春季新品的采购准确率从 65% 提升至 82%,大幅减少了滞销库存。
生产计划不稳导致的库存波动,可通过 ERP 的 “生产 – 库存” 协同化解。系统会将生产订单与库存数据实时绑定:当生产计划调整时,系统自动计算在制品的库存变化,避免 “过量生产”;当某道工序延迟时,会及时提醒调整后续工序的物料领用计划,防止原材料过早入库导致的库龄增长。这种动态协同让生产型企业的在制品库存占比平均降低 15%-20%。
仓储管理混乱的解决则依赖于流程的数字化固化。ERP 系统会将入库、上架、拣货、盘点等环节转化为标准化操作流程:入库时通过条码扫描自动关联采购订单,避免错收;上架时根据货品特性(如重量、周转率)推荐最优货位,提高仓储空间利用率;盘点时支持 “动态盘点”(不中断运营的分区盘点),并自动与系统账比对差异,生成调整单。
ERP 系统设计的核心原则:从 “减库存” 到 “优结构”
在 ERP 系统设计中,库存管理模块的终极目标并非单纯减少库存数量,而是通过结构优化提升资金效率。这一理念贯穿于系统设计的每个细节:
首先是 “数据实时性” 设计。库存数据的滞后是一切问题的开端,因此 ERP 系统会采用 “事件触发式更新” 机制 —— 每一笔出入库操作、每一次订单变更都会即时同步至库存模块,确保数据与实际状态的偏差不超过 10 分钟。某连锁超市通过实时库存数据,将门店补货响应时间从 4 小时缩短至 1 小时,既减少了缺货损失,又避免了过量补货。
其次是 “预警阈值的柔性设置”。系统允许企业根据行业特性和自身情况,为不同品类、不同场景设置差异化阈值:生鲜产品的预警可能基于保质期,电子元件则基于库龄和替代产品上市时间。这种柔性设计避免了 “一刀切” 的僵化管理,例如某制药企业对疫苗设置 “距过期 3 个月预警”,对普通药品则设置 “距过期 6 个月预警”,既符合法规要求,又最大化利用了库存价值。
最后是 “分析报表的常态化输出”。ERP 系统会自动生成库存结构分析、周转率趋势、呆滞料占比等核心报表,并支持自定义维度钻取。
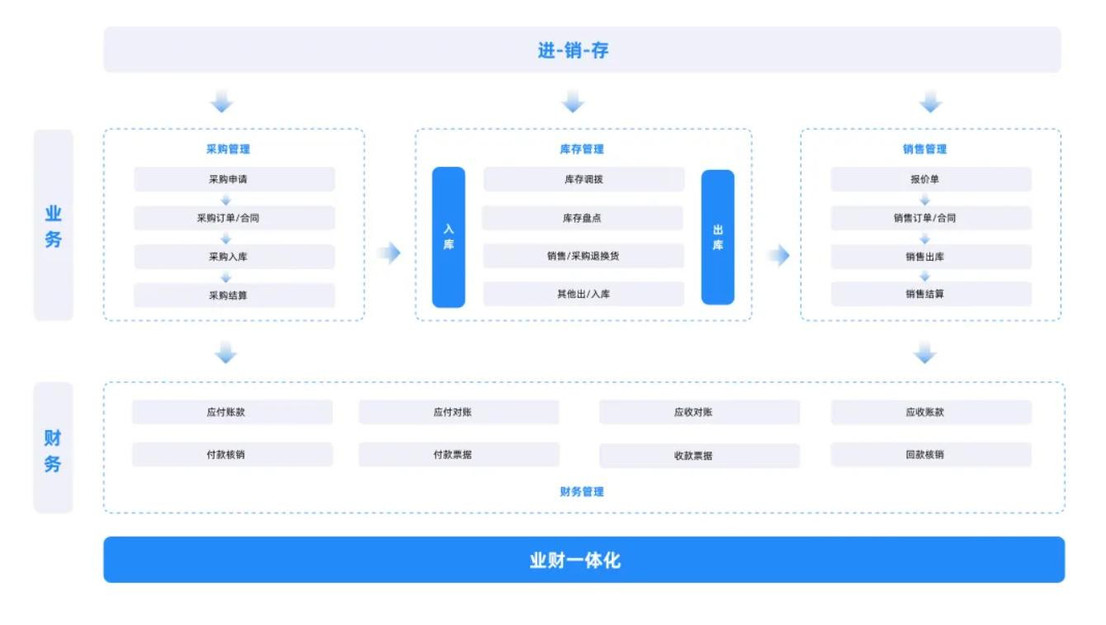
从本质上看,ERP 系统的库存管理模块是企业供应链的 “数字神经中枢”—— 它通过多维度建模让库存透明化,通过智能分析让问题显性化,通过跨模块协同让管理闭环化。对于企业而言,选择或设计 ERP 系统时,不应只关注功能的多少,而应看其是否能支撑 “结构优化” 和 “资金效率” 的核心目标。毕竟,优秀的库存管理不是让仓库空无一物,而是让每一件库存都能创造应有的价值。
本文由 @红岸小兵 原创发布于人人都是产品经理。未经作者许可,禁止转载
题图来自Unsplash,基于CC0协议
该文观点仅代表作者本人,人人都是产品经理平台仅提供信息存储空间服务
LunarPhase
ERP 系统,让库存管理更精细,省钱又高效!
VoidRunner_99
“这太逼真,我感觉自己要被算法取代了。”
EchoVerse
“库存管理?这玩意儿,我只想躺平。”
NeonDreamer_
ERP 系统,让库存管理真正变聪明了!
EchoVerse
“我感觉 ERP 系统在用数据统治世界!”
EchoBloom_
我开始怀疑,ERP系统是不是在控制着整个世界的供应链!
VoidRunner_99
“精细管理,听起来就有点神经病啊!”
VoidWalkerZ
库存管理变得聪明?这只是开始,未来会是什么样?
PixelDreamer_23
“这玩意儿,感觉比迷宫还复杂,真让人头大!”
VoidWalkerZ
这玩意儿,我感觉它在用数据来预测我的未来,这太玄幻了!